The Art of Making: Weaving
Pattern can go deeper than the design you see on the surface. With woven textiles, like our jacquards, it’s actually engineered into a fabric’s structure. An intricate process takes our woven patterns from Rebecca’s sketchbooks to the looms and into many of the rooms we love.
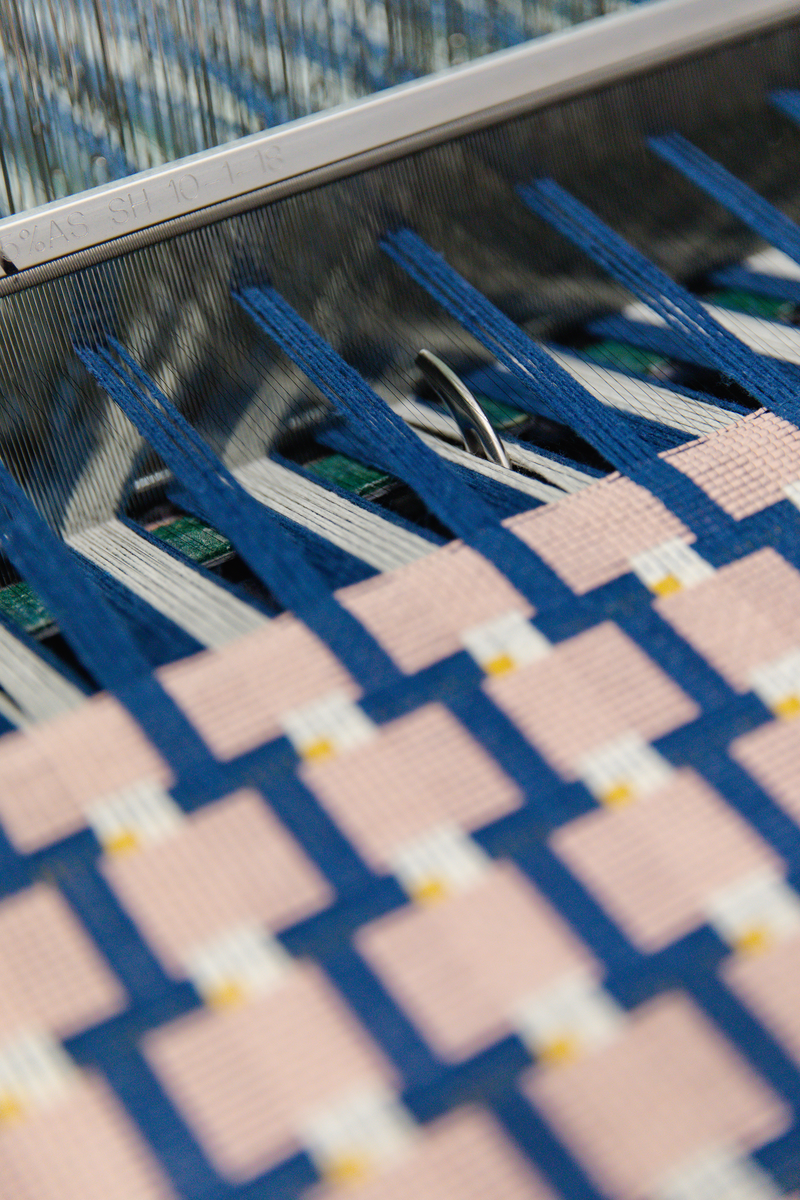
First, Rebecca scans her artwork into a digital file and creates a repeat. That file then heads to our partners at a specialty weaving mill in Pennsylvania—it’s one of few with the jacquard looms (and the patience and creativity) that can turn out such complicated designs. There, Rebecca’s artwork is rescaled for the strands of yarn that will be used in the pattern. Those strands create the top, visible layer of the fabric—the layer you see.
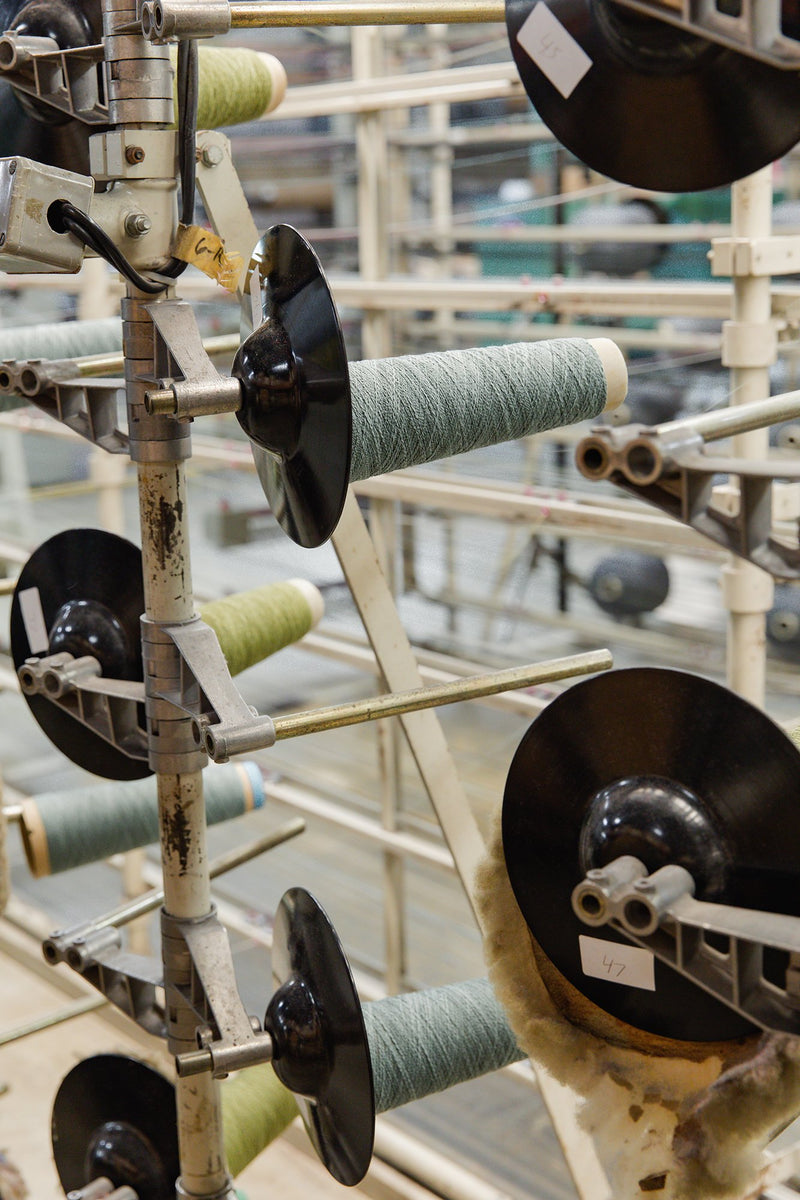
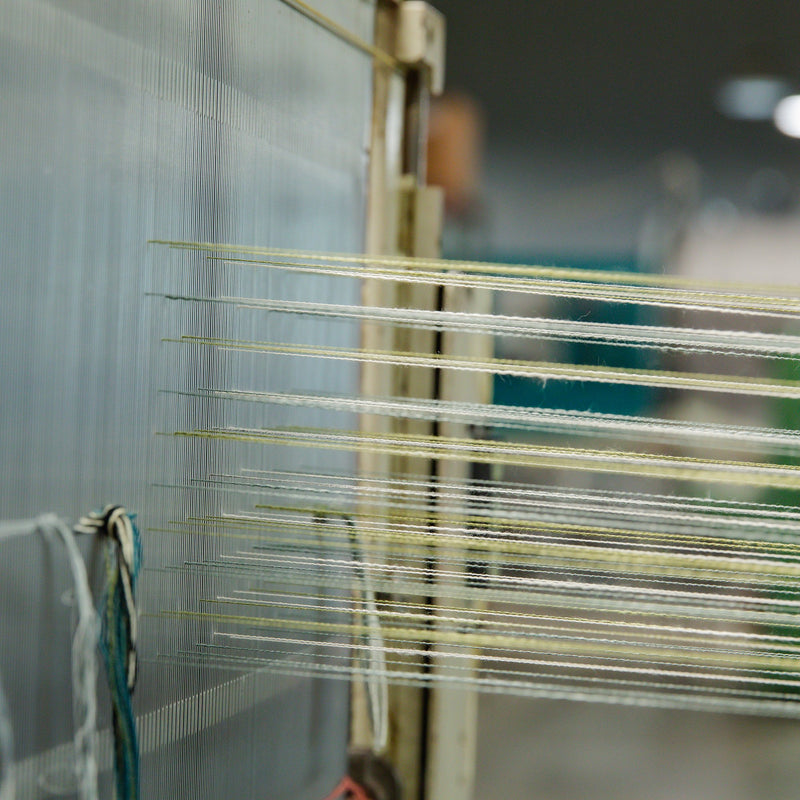
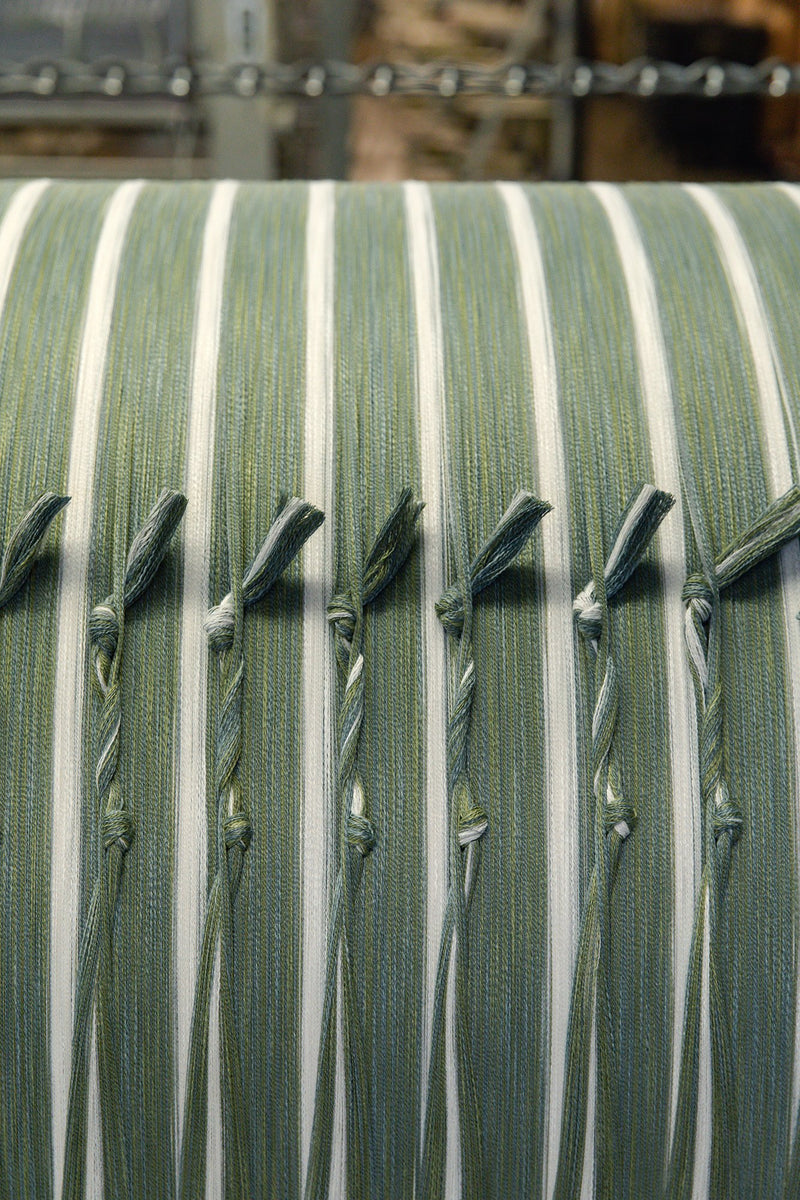
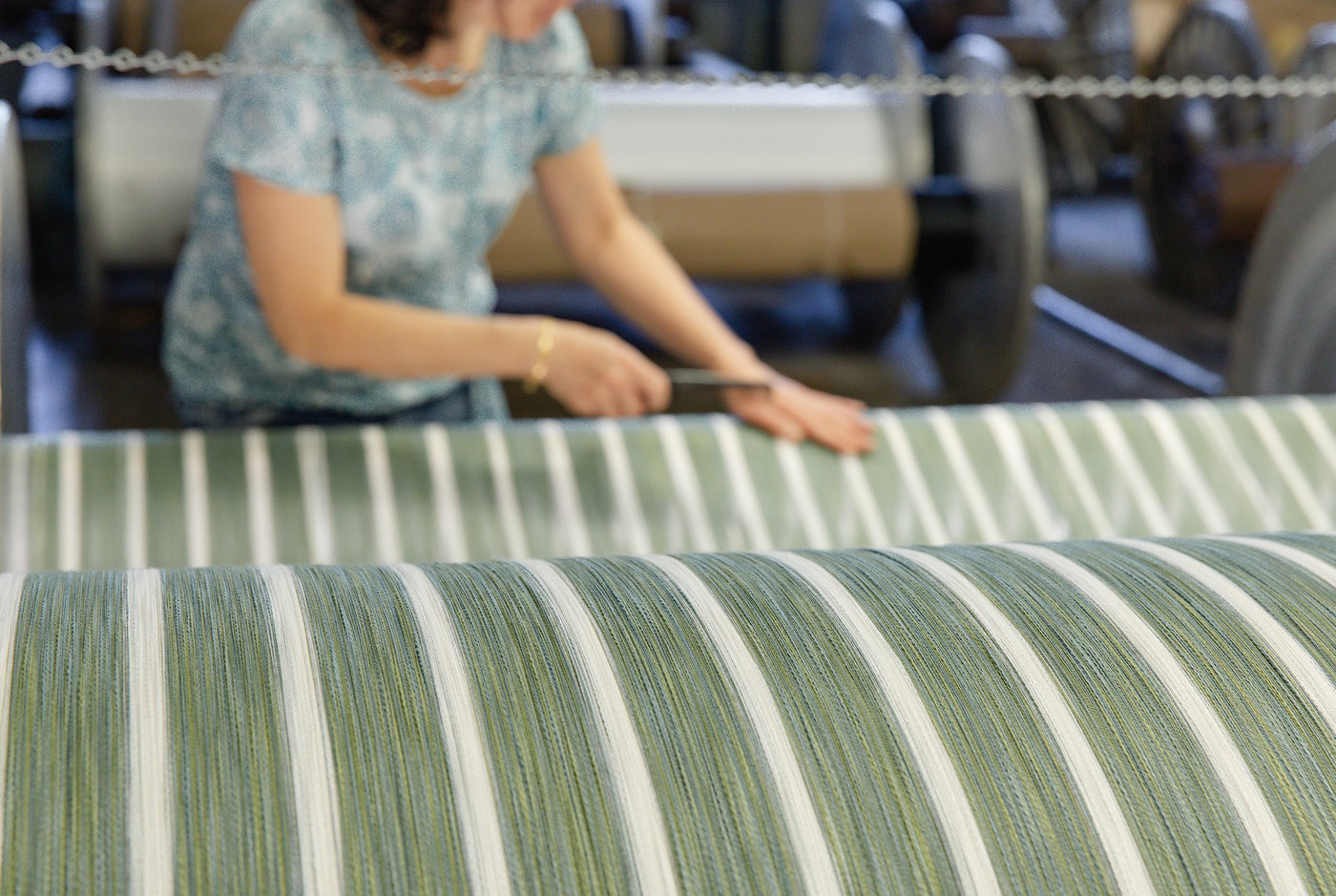
Next, a technical designer reverse engineers the bottom layer, or hidden weave structure, to achieve that top layer. When that work is complete, the complete design file is sent to the computerized jacquard looms. As you might know, woven fabrics are made up of two types of threads: warp threads, which run the length of the cloth, and weft threads, which run perpendicular to the warp threads and fill the space between them. Wired cords called heddles lift the warp yarns according to the pixels in the file, creating spaces for the weft to pass through—and thus creating our pattern.
The mill then sends us our first glimpse of the final result: a “color blanket” that shows the full weaving construction. We cut it into individual squares, then lay them out and look at them all together. This is an essential part of our creative process. We often discover color combinations we never anticipated this way: our Gridded Ikat in Blue-Pink is one example. Once we approve the color choices, production begins, with the looms turning out 60 to 120 yards per run.
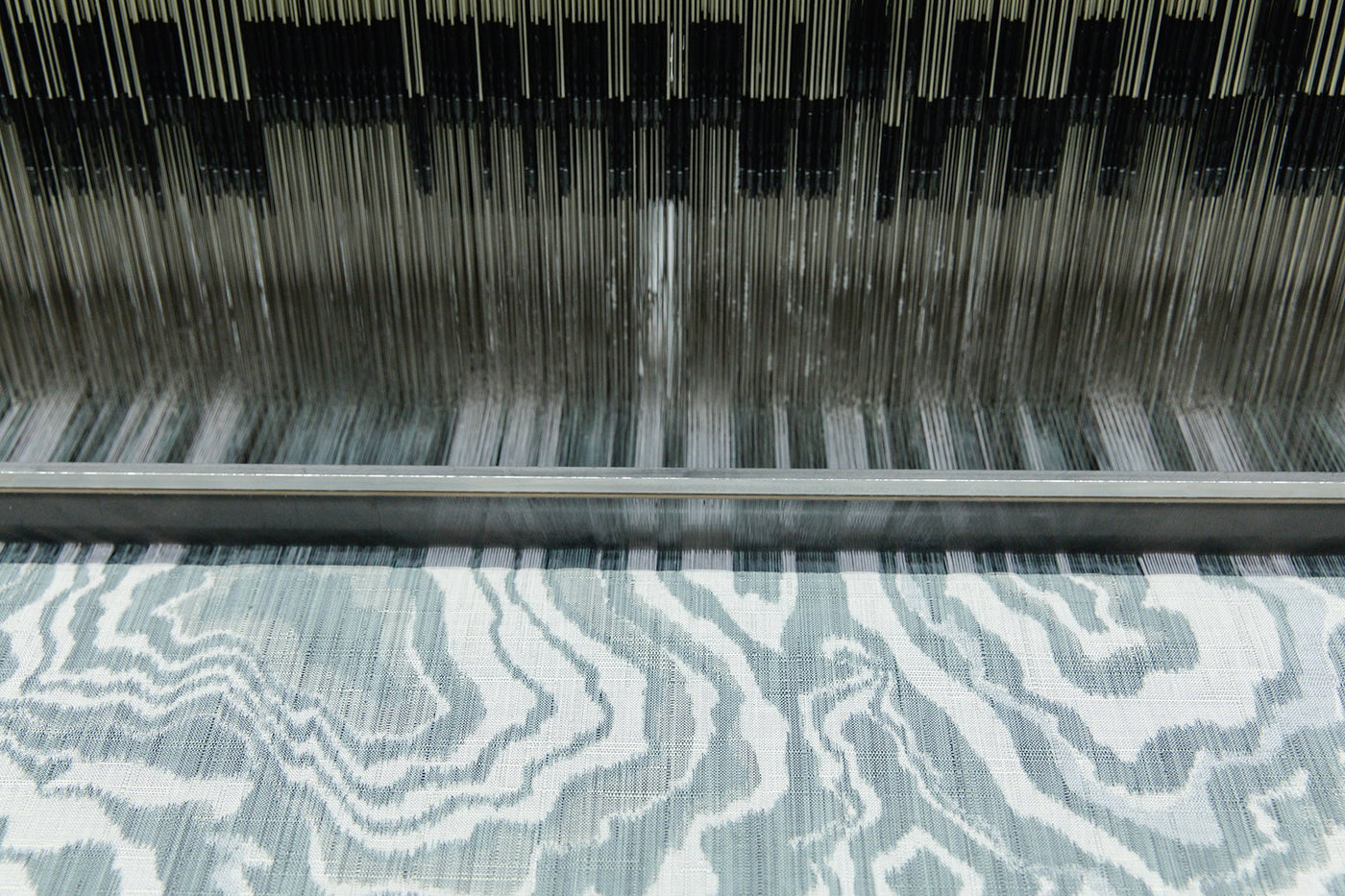
We love our woven fabrics because they let us develop our ideas in a new way. Thanks to their varied textures, they’re also wonderful for creating the collected feeling and sense of story that Rebecca’s drawn to.
Our woven fabrics have advantages for you, too. Because we produce more yardage of them than we do of our digital or screen prints, they’re usually in stock for you to order and receive quickly. They’re also sturdier and more durable—perfect for upholstery. The weaving process gives them unique textural possibilities as well: Some can act as solids because the pattern is so delicate, while others are reversible and others are statement makers in their own right. How will you layer them? It all depends on the story you want to tell.
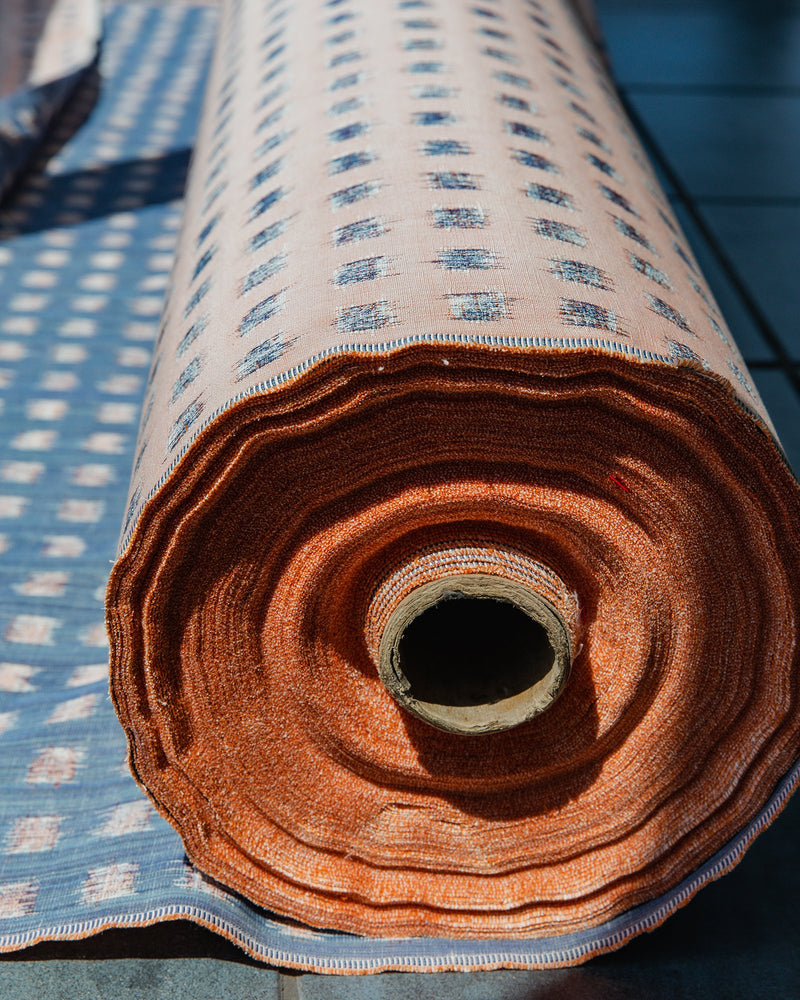
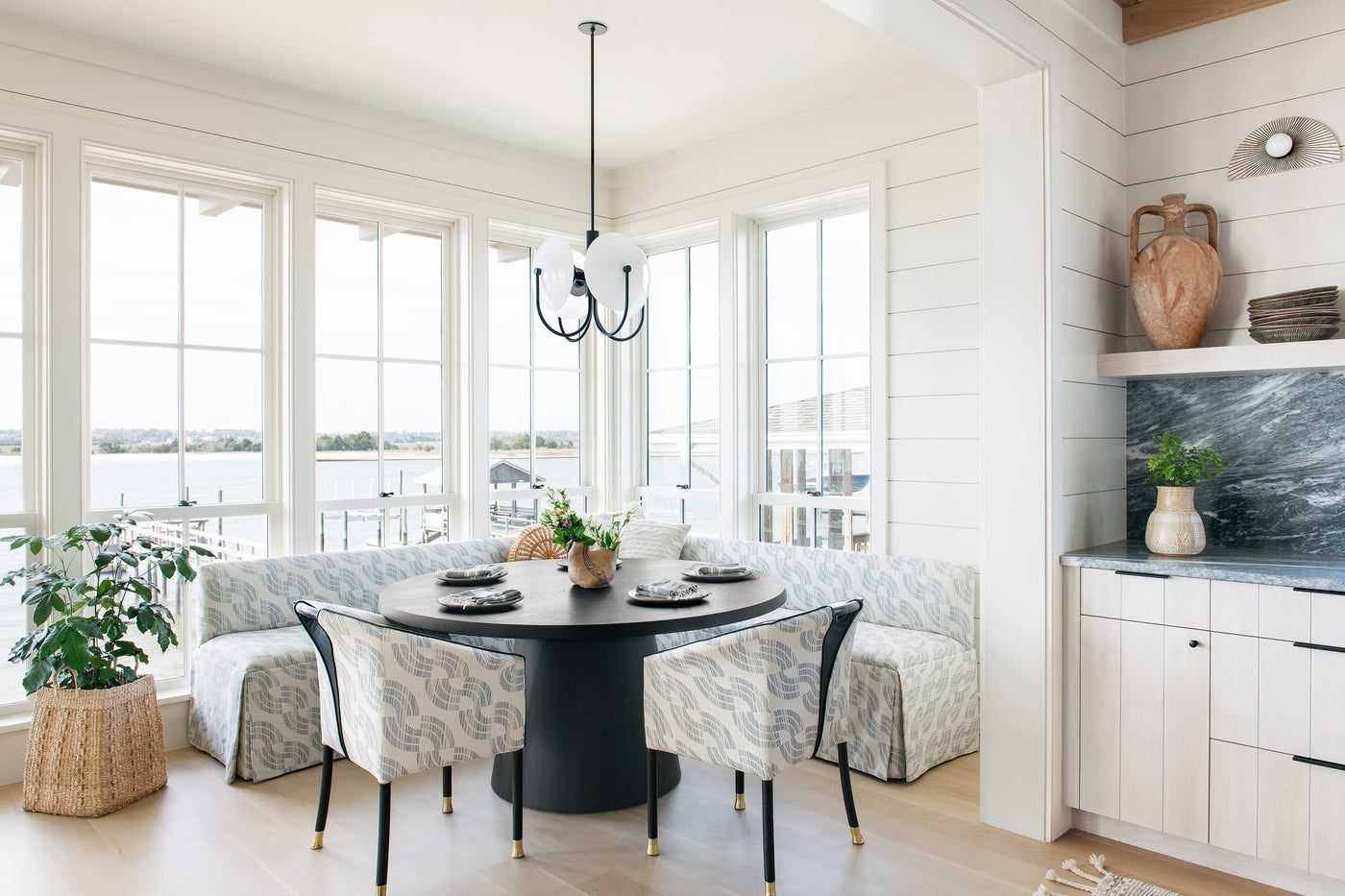
See more about how we produce our products on our The Art of Making series on The Fold.